£0.00
0Bespoke high temperature heat treatment wheels
The application
Our client for this project was Fabwell Ltd. They are one of the UK’s biggest design and manufacture specialists of heat and corrosion resistant alloy fabrications, furnace spares, repairs and modifications.
The requirement was to design and manufacture a charging carriage running on rail sections, feeding a copper annealing furnace in a high-volume production facility.
The challenge
Crucially, the wheels used needed to withstand a temperature of 250 degrees centigrade for a period of up to five minutes to resist radiated heat when the furnace door is opened. The wheels are required to guide the carriage accurately to negate probable alignment issues. The carriage needed to travel in a straight line using flanged rail wheels. The load capacity requirement of the carriage was five tons.
The bearings needed to withstand elevated temperatures and have an accessible greasing facility. A ‘bolt on solution’ was required to ensure a minimum installation time on site.
The project needed to be completed within a set timeframe to hit the client’s factory shutdown window.
BIL Group solution
We used double flanged wheel sets to provide guidance on the rail. These wheels were manufactured from high tensile grade steel and fitted with high temperature rolling element kiln car bearings, installed with high temperature grease and a ‘through axle’ greasing facility.
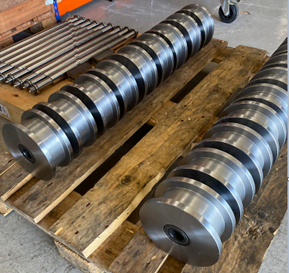
The bolt-on capability was achieved using pinch bracket type mounting blocks, positioned on a common axle, with the wheels mounted at each end and secured with a lock nut and tab washer arrangement.
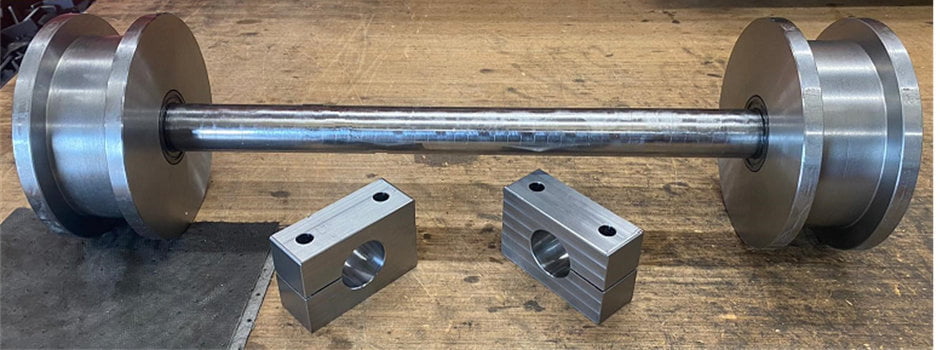
Bespoke axles gun-drilled and cross-drilled provided a through-axle greasing facility, with the grease nipple positioned at the end of the axle to make it easy to lubricate from an accessible location.
Wheel sets were mounted in series along the length of the carriage to spread the five-ton load and to offer support whilst maintaining consistent guidance on the rail tracks.
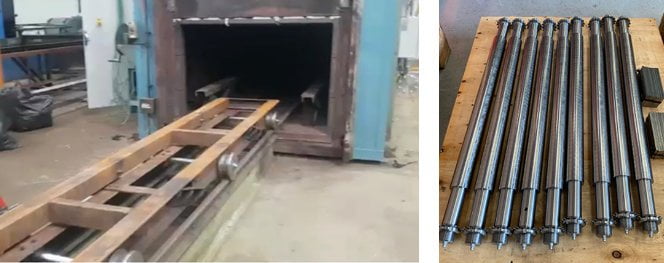
Axle pinch brackets enabled quick and easy installation using a simple four-bolt fixing method which located precisely into pre-drilled holes on the underside of the carriage fabrication.
Outcomes achieved
The solution we provided allowed significant energy savings and increased productivity levels to be gained through improved cycle times, allowing faster throughput of heat-treated materials, which in turn resulted in savings on gas consumption due to reduction in heat loss through furnace doors needing to be open for less time.
Paul Dickens, Managing Director at Fabwell Ltd, commented after the installation had been completed, “I am very pleased with the outcome of this project and look forward to working with BIL on future projects.”
If you are searching for an engineering solution to an existing process or business issue or if you have product development ideas that you would like to explore further, please contact us to discuss how we might be able to assist you. Our innovative and experienced bespoke engineering team would be delighted to hear from you.