£0.00
0Flanged Wheels – keeping you safely on track
In this post we’re taking a closer look at flanged wheels and their uses.
Think of flanged wheels and you probably picture William Jessop’s cast iron wheels, manufactured for railroading and made specifically for high-speed use. This is the most popular vision of a flanged wheel but there are many other options available for varied applications, especially if speed is not the number one priority and you are dealing with variables such as direction of travel, durability and weight loading.
What are flanged wheels?
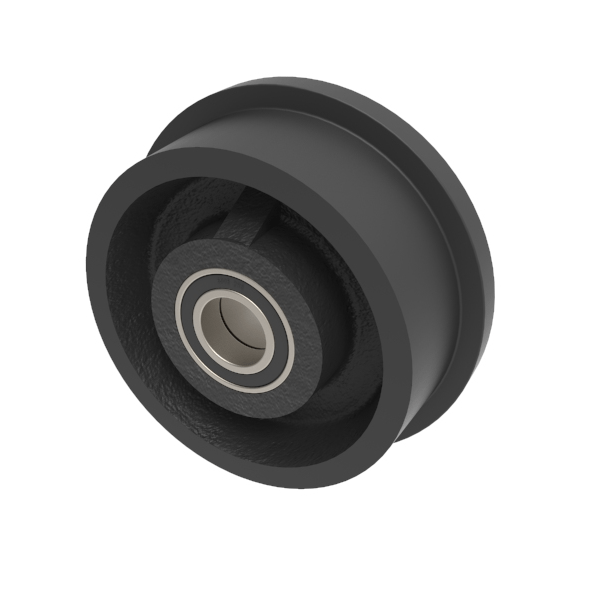
A flanged wheel is also commonly known by other terms such as track wheels, rail wheels, and channel wheels.
Flanged wheels are generally made up of a steel or cast outer tread and the term ‘flange’ refers to the protruding edge on the circumference of the wheel.
The flange section is carefully designed to keep the wheel on a track or rail and to enable it to become self-guiding.
Typically the flat surface of the wheel – away from the flange – is manufactured to be wider than the track itself. The reason for this is it allows a tolerance for any movement or pitch in the rail.
Often you will see flanged wheels with a tapered tread when used in pairs. The tapered profile provides centring on the rail. Naturally the wheel wants to pull against rail, the taper diverts the wheel towards carriage instead, allowing it to move freely in the direction of travel.
Flanged wheels can be manufactured with a plain bore, keyway or with bearings.
A ‘keywayed’ wheel means that the wheel will be driven with a motor or chain drive. This will be on a solid axle connected to the wheel that rotates, driving both wheels in the same direction, at the same speed.
Bearing wheels are often used for free-wheeling or idling.
Materials used for flanged wheel manufacture
Most flanged wheels are manufactured from either cast iron, machined steel or nylon material.
The main reason for manufacturing from cast iron is that this is most economical compared with machined steel for light to medium duty weight loadings, but they do come with a limited service life in comparison.
Machined steel flanged wheels are more suitable for high rotational speeds and can withstand potential shock loading much better than cast iron alternatives.
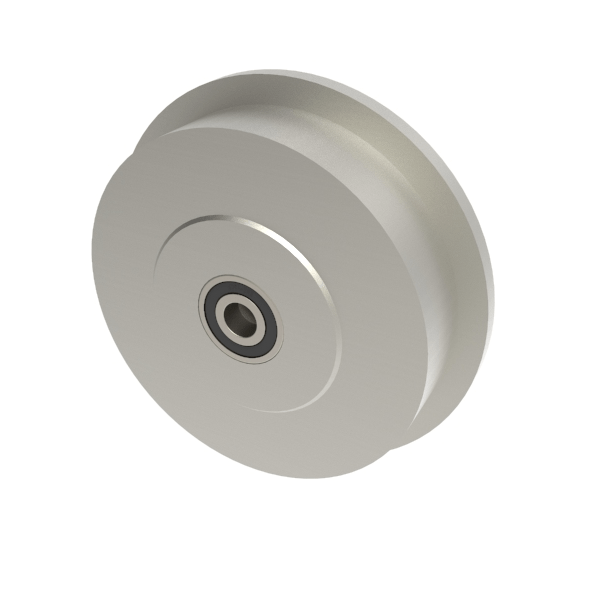
Steel is a more robust material making it a better overall option for industrial applications and will prove to be more durable, especially where more contact between track and flange will occur.
The reason for use of a nylon flanged wheel is that it provides protection against any corrosion as opposed to iron or steel of course.
Where overall weight is an issue, nylon is also a good alternative due to its lighter weight properties.
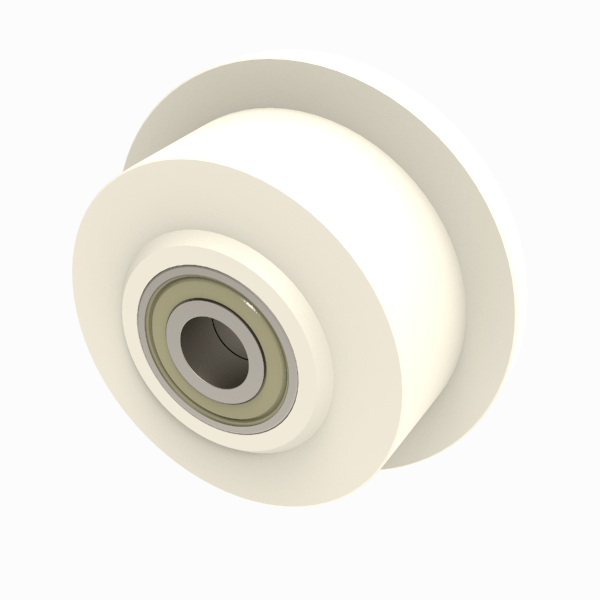
Nylon will also often be found on applications where distances are much shorter.
Nylon flanged wheels are also used within food related environments where contamination needs to be contained.
Types of flanged wheel
Single Flange wheels
Single flanged wheels are generally used in pairs on common axles opposing one another. The rail in this type of application, needs to have a constant and accurate pitch along the entire length to prevent binding or ‘crabbing’.
The tread is machined with a taper to provide centring of pairs when running on convex crown profiled rails.
A single flange wheel is exactly that – i.e. the wheel only has a single flange around the circumference of one side of the wheel.
Single Flanged Wheels are often used on rail / trolley applications and are fixed to an axle which means a single flanged wheel on each side of the axle is often enough to prevent unwanted movement in either direction.
When wheels are running on flat surfaces – such as rectangular flat bar, or on the top on a beam – the tread can be manufactured flat and parallel, to mate with the running surface and achieve maximum contact area, with the addition of a taper machined on the inner flange face to provide a running clearance.
Double flange wheels
Double flange wheels are similar in design to a single flanged wheel but as the name implies they have an additional flange at the opposite side of the wheel providing a fixed middle tread section.
A taper is machined on the inner face of the flange on each side, to provide running clearance and minimise binding.
Rather than relying on an axle to fix the position like a single flanged wheel, a double flange helps keep each wheel independently on track. This proves to be popular where travelling over larger distance.
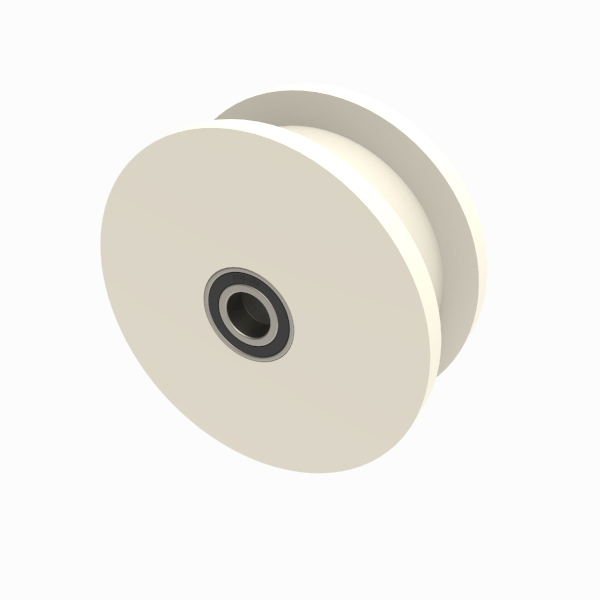
Double flanged wheels are similar in design to a single flanged wheel but as the name implies they have an additional flange at the opposite side of the wheel providing a fixed middle tread section.
A taper is machined on the inner face of the flange on each side, to provide running clearance and minimise binding.
It is possible to utilise two double flange wheels together however this would be for very slow moving applications over short distances and the rail would have to be aligned perfectly, eliminating risk of the wheels binding.
To ensure maximum load rating can be achieved for each wheel the full tread width needs to be in contact with the rail, track, or channel. If not, the wheel may force to much weight onto one sided thus reducing the capacity.
Common applications
There are many applications for flanged wheels most of which however involve a rail and some form of transportation.
Applications can include but are not limited to:
- Transfer carriages
- Shuttle carriages
- Tunnelling
- Process machinery
- Water industry / Sewage Treatment
- Recycling
- Brick production
- Ceramics & pottery production
- Heat treatment furnaces & ovens
Get expert advice before you buy flanged wheels
Unless you know exactly what you require you should take expert advice before buying flanged wheels. It is essential to understand the function of your wheels and to understand the requirements fully. This will avoid unwanted downtime, broken components and will save costs, improve productivity and provide maximum efficiency and safety.
Flanged wheels typically need to be considered carefully in regard to material type, weight loading, duration and application criteria, so discussing your requirements in detail with technical sales engineers who understand the applications and your requirement, is highly recommended.
BIL Group have a wealth of experience and expertise in this field, manufacturing and supplying standard and bespoke made wheels to many industries for the applications mentioned in this article and more. If you need assistance to specify or purchase flanged wheels, please contact us. We are ready to help and advise you and we would be delighted to hear from you.